Natural Dyes
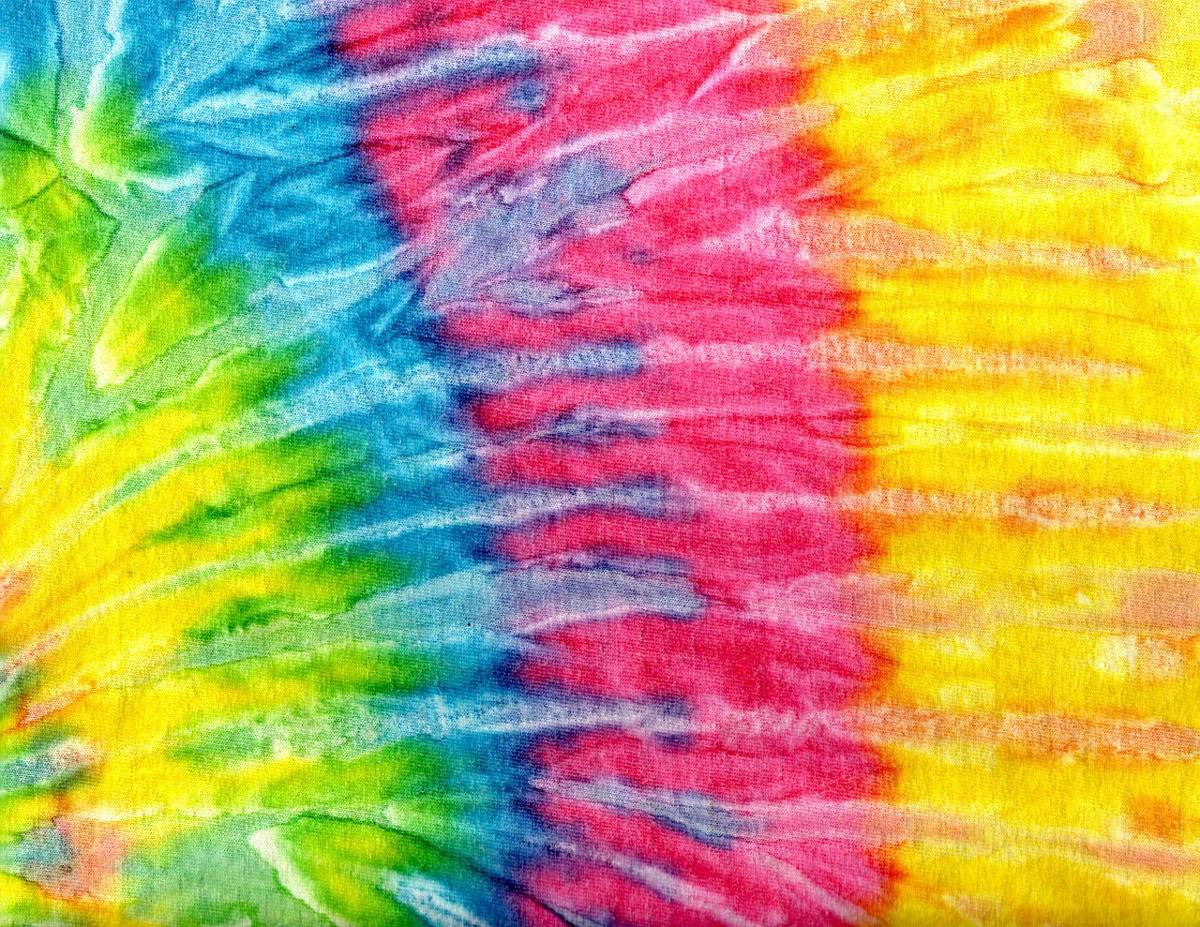
It is believed that our color selections are mostly unconscious, yet they influence every moment of our life. Many of us have our favorite colors and often prefer wearing clothes of that particular color. Though the colors that we are fascinated with over a long period of time are in one way or another connected to our personality type, our strengths and weaknesses, as well as our potential in life. But wearing your selective styles of garments in synthetic dyes and natural color dyes is a different experience altogether.
Dyeing is a very ancient art. It was practiced during the Bronze Age in Europe, Asia and many other regions and countries. Primitive dyeing methods involved sticking plants to fabric or rubbing crushed pigments to the cloth. The procedures became more sophisticated with time as techniques of applying natural dyes from crushed fruits, berries and other plants, which were boiled into the fabric and gave light and water fastness, were developed.
Some of the recognized olden dyes include madder, a red dye made from the roots of the Rubia tinctorum, blue indigo from the leaves of Indigofera tinctoria, yellow from the stigmas of the saffron plant, turmeric and dogwood pulp. The first application of the blue dye, woad, favorite of the Ancient Britons, may have originated in Palestine where it was found largely. Though many natural dyes are made from metals, for example natural black color is made from recycled horseshoes and molasses, red is made from aluminum sulphate and red earth.
Eco-friendly, Economical Aspects of Dye
Today, dyeing has become a specialized science and has a very complex functioning. Almost all dye stuffs are now made from synthetic compounds. This denotes that costs have highly decreased and many application and wear characteristics have largely improved. But many practitioners of the craft of natural dying still believe that natural dyes have a better visual quality, which is much more delightful to the eye. In the West, natural dyeing is now used only in handcrafts, whereas synthetic dyes are used in all commercial aspects. Some craft spinners, weavers and knitters use natural dyes for making specific features of their work. Though, in many of the developing countries natural dyes can provide not only a prosperous and wide-ranging source of dyestuff, but also the likelihood of an income through sustainable harvest and sale of these dye plants. Many dyes are prepared from tree waste or can be simply grown in market gardens. Natural dyes can provide attractive options, where relatively expensive synthetic dyes, mordant (fixatives) and other additives are imported.
The knowledge needed for finding and extracting such dyes and mordant does often not exist, as far-reaching research work is needed to recognize appropriate plants, minerals, etc. For example, there are a variety of plants available for making natural dyes in Zambia, but because of lack of knowledge of the practice implicated in harvesting and processing the plants; little utilization is done for this natural resource. In some countries, such as India, Nigeria and Liberia, where this research has been done extensively, or where there is easy accessibility of natural dyeing, natural dyes and mordant are used widely.
The main colors used are black from iron sulphate, blue from the Indigo plant and yellow from turmeric and pomegranate rind and peels. The rest of the colors are obtained from these kinds of natural resources as mentioned in the table.
Sources of Natural Dyes
Specialist plant and animal sources Many plants and some animals have been identified for making natural dyes. A range of parts of plants like roots, stems, barks, leaves, fruits and seeds are generally used. By-products (Particularly lac dye): The lac industry provides lac dye as a by-product, which is taken from the effluent. Likewise from cassia tora, utilized in gum production, a brown dye is obtained as a by-product.
Chemical mixture: It is a mixture of dyes of molecular structure similar to those of natural dyes. Cell or tissue culture by DNA transfer technology: A few fungi such as Drechslera and Trichoderma make anthraquinone derivatives. Anthraquinone is a significant type of dye, where exploiting the fungi would be helpful over their chemical mixtures.
Natural Dyestuffs
Since olden times, dyestuffs and dyeing are used in textiles and garments. Nature gives prosperity to plants which in turn offer their color for the purpose of dyeing, many being used since ancient times.
More or less any organic material will create a color when boiled in a dye-bath, but only few plants will give a color that will work as a dye. The plants provided in Table 1 are a selection of a few plants, which are widely used traditionally as natural dyers. Natural dyes are obtained from the following categories:
Leaves and stems
Twigs and pruning
Flower heads
Barks
Roots
Outer skins, hulls and husks
Heartwoods and wood shavings
Berries and seeds
Lichens
Insect dyes
Few examples of obtaining natural dyes from various sources
Indigo:
Still used by many block printers and dyers in the villages of India, Indigo gives shades of blue and some greens. Workers today utilize the same method used since olden times for natural indigo dyeing. Indigo is made in large vats made of clay that can contain at least 1000 liters of dye. These are sunken into the ground and this gives a consistent temperature to make the dye work. The indigo dye bath is prepared by using molasses and lime, and then preserved for around six months until it is exhausted. The cloth is constantly dipped and immersed in the vat and then exposed to the air to make different intensities of blue color.
White patterns in textiles are retained by making a paste from clay mixed with wheat chaff and tree gum. The paste restricts the dye from entering the covered areas. Indigo simply binds and connects with the fibres and through washing and friction some of the indigo molecules break away. This is why Indigo rubs off on your skin and can also be cleaned easily.
Turmeric & Pomegranate:
Boiled pomegranate peels and turmeric powder are mixed to make yellow color. It is also used for over dying blue fabric to create green color.
Natural Black Dying:
In various parts of the world, the color black is made in various ways and different shades and hues. As a result, a variety of shades varying from dark plum to blue black and snake black to soot black are obtained. Indian dyes are well-known for their special application of alum and iron metallic salts that capture red and black. Iron is utilized as a mordant for black in dyeing with madder and other dying plants. In India, the syahi (mordant) is made by fermenting iron or iron oxide in rusted iron in molasses (gur), tannin, or jaggery for a period of several days. The craftsmen judge when the mordant is ready by the familiar tang in the smell. The mordant has to be applied at the proper moment of fermentation if the best performance is to be achieved. After the process a reddish black color is obtained. Jet black is obtained by adding any yellow or yellowish green mordant dye to the process. When mixed with madder, it gives red.
Mordant
Only some natural dyes are color-fast with fibres. Mordant are substances which are applied to fix a dye to the fibres. They also increase the take-up quality of the fabric and support it by increasing color and light-fastness. Many natural dyes, for example indigo, set without the help of a mordant. Such dyes are defined as ¡¥substantive dyes¡¦. Other dyes, such as madder and weld, have a limited fastness and the color lightens with cleaning and exposure to light.
Mordant are found in nature. For example, wood ash or stale urine may have been utilized as an alkali mordant and acids could be found in acidic fruits or rhubarb leaves. Nowadays the majority natural dyers use chemical mordant such as alum, copper sulphate, iron or chrome.
Mordant are made in solution, usually with the addition of an ‘assistant’ which increases the fixing of the mordant to the yarn or fibre. In general, the most commonly used mordant is alum, which is normally applied with cream of tartar as an additive or assistant. Other mordant are:
. Iron (ferrous sulphate)
. Tin (stannous chloride)
. Chrome (bichromate of potash)
. Copper sulphate
. Tannic acid
. Oxalic acid Using a variety of mordant with the same dyestuff can create different shades, for example;
. Iron is used as a ‘saddener’ and also to darken colors.
. Copper sulphate darkens and can also provide shades which are otherwise very difficult to obtain.
. Tin perks up colors.
. Tannic acid used with other mordant adds brightness.
. Chrome is good for obtaining yellows.
. Oxalic acid is ideal for extracting blues from berries.
. Cream of Tartar is not really a mordant, but is applied to provide luster to wool.
Mordant are normally poisonous, so it is advisable that in the dye-house they should be kept at the right place. When working with mordant, one should always wear protective clothing and avoid breathing the fumes. The mordant can be added before, during or after the dyeing stage, although much care should be taken prior to dyeing. It is appropriate to follow the instructions according to the use and process.
As against these mordant, there are a number of plants and minerals which can give good mordant. Some of the common options are as mentioned below.
Some plants, such as mosses and tea, contain a small amount of aluminum. This can be used as an alternative to alum. It is hard to recognize how much quantity of aluminum will be present. . Iron water can be used as an option for ferrous sulphate.
. Oak galls or sumac leaves can be used as an alternate to tannic acid.
. Rhubarb leaves possess oxalic acid.
The selection of mordant for a specific plant is dependent upon the material with which it will be used. It is necessary to ensure a recipe before using a plant. It is suggested that plants be grown particularly for the use of dyeing.
Textile Fibers and Dyeing
Natural dyes can be used for majority types of material or fibre, but the standard of success in terms of fastness and clarity of color differs significantly. Users of natural dyes, though, are likely to also use natural fibres. Natural fibres are available mainly in two distinct origins, animal origin or vegetable origin. Fibres from an animal origin cover wool, silk, mohair and alpaca, as well as some others which are less accepted. While animal fibres are based on proteins, natural dyes have a well-built attraction to fibres of animal origin, particularly wool, silk and mohair and the outcome of these fibres are normally excellent. Fibres of plant origin include cotton, flax or linen, ramie, jute, hemp and many others. Plant fibres possess cellulose as their basic ingredient. Natural dyeing of such plant based textiles can be less gleeful than their animal equivalent. Various mordant methods are used for each category. When a mixture of fibre of both animal and plant origin is being dyed, then a method should be selected which will stress on the fibre which is required to be dominant.
Dye Testing
It is always beneficial to test the dye, which is to be applied, on a sample of the yarn or fabric to be dyed. The result will depend on the fabric, the mordant that has been used and dye that has been selected. It can then be tested for light, water and washing fastness by applying simple standard test methods. Below explains a simple test for washing fastness. Similar tests are available for water and light fastness. Treatment of the plant can be done in many ways, but usually it is done in the form of soaking or boiling the plant to extract the dye. Few plants, such as indigo, require a unique preparation for application; few require boiling to extract their dye, while others can merely be soaked for long periods.
Test Procedure for Fastness to Washing
To test fastness one must follow a step by step procedure:
1. Take two pieces of fabric of 5cm by 5cm, one of which is undyed cotton and the other undyed wool. Stitch them closely at one side.
2. Take some sample strips of the dyed yarn and spread them evenly between the two pieces of cloth, so that they overlap both sides. If dyed fibre is being tested, a combed sample can be used as an alternate option of the yarn.
3. Sew around all four sides of the cloth so that the yarn is kept in place.
4. Make a similar sample with dyed materials that has suitable properties and put them in two jars with screw lids with a solution of 5gm per liter detergent solution at 30 degree Celsius.
5. Agitate the two jars for 30 minutes, then remove the fabrics and wash them in clean water for 5 minutes. Open the stitches and take separate the pieces to dry in air.
Examination: 6. Put the dyed yarn next to a sample of the same material which has not been tested, and compare the change that has taken place. Compare it also with the control sample with satisfactory properties. If the dyeing being tested shows equal or less variation then it is a good and satisfactory sample.
7. Put the wool and cotton clothes next to samples of the same material which have not been tested and analyze them with the clothes that have been tested with satisfactory dyeing. Equal or less staining illustrates equal or better fastness.
The Procedure of Dyeing
Function of The Dye
Dyeing can be done at any of the following steps in the textile production stage:
. The fibres can be dyed before being spun. Fibre dyeing gives a deep penetration of the dye into the fibre, providing even color and outstanding color-fastness.
. After spinning, the yarn can be dyed, but before the product is woven or otherwise fabricated. This is referred as Package dyeing.
. Before the fabric is finished, it can be dyed in piece (piece dyeing). This process gives producers the opportunity to make fabrics in their natural colors, and then dye them to order.
. Fabrics of two or more fibres can be dyed in cross-dyeing, so that each fibre accepts a different dyestuff and becomes a different color, through the use of suitable dye stuffs for each fibre. It is necessary to correctly identify the fibre or other fabric to be made before dyeing commences.
Dyeing Methods
There are a many methods used to dye to a fabric. Though the most common method applied for natural dyes is the vat method, there are practices which have been developed to allow patterns to be built-in during the process of dyeing. Applying natural dyes is a complicated art and the skills needed for using natural dyes are gained with an experience of many years.
Vat Dyeing
In this easiest way of dyeing, a textile material is dipped in dye and slowly brought to boil. Alternatively, the fibre is permitted to sit and soak for few hours or days. In this period, agitation is necessary to facilitate complete penetration of the textile by the dyestuff. According to the type of fabric and dyestuff applied, few salts or acids may be added to help absorption of the dye. The main problem in dyeing mixed yarns and fabrics is to receive the same color in both fibres. Cotton fibres may, for example absorbs dyes fast, while the wool fibres will have to be boiled over a so long time to achieve the same depth of shade. This could lead to a noteworthy damage to the material. In this case a chemical compound would be needed to be applied to hold back the rate at which the cotton fibre receives the dyestuff. The amount of dyestuff which is applied is normally provided in the recipe. It is normally quoted as a percentage weight of the fabric to be dyed.
Below Illustrates a Standard, Simple Recipe for Dyeing Using Natural Dyestuff
Recipe of dyeing wool with onion skins
Fabric: appropriate for wool or other animal (protein) a fibres.
You will require:
• natural wool – 100 grams
• onion skins (the dry, brown, outer skins) – 30 grams
• alum (the mordant) – 8 grams
• cream of tartar (the assistant) – 7 grams
• liquid detergent (the scouring agent)
• water supply
If a larger quantity of wool is to be dyed, increase the quantities to a proportionate degree. Weigh the wool. All weights mentioned above are comparative to the dry weight of the wool. Skeins of wool are tied loosely at many places to stop tangling. In this case the recipe calls for 30% dyestuff i.e. the weight of the dyestuff is 30% than that of the fabric to be dyed.
The wool should be scoured, which means it should be fully clean. For this, the wool needs to be soaked all night in a liquid detergent solution. Then rinse the wool well and smoothly press out the extra water. Use lukewarm water and avoid sudden variations in temperature of the water which make the wool felt or mat. The skein will be the mordant. Dissolve alum and cream of tartar in a little hot water and then add the same solution to cool water in the mordant pot. Dip the wetted yarn and then put the pot on the heat source. Gradually increase the temperature to 82°C and boil for 45 minutes. Let it cool after which remove the wool and rinse well.
To prepare the dye bath, put the onion skins in the dye pan and cover them with water. Gradually heat the dye bath to the boiling point. Boil for about 45 minutes, by which time the whole color should have been extracted from the onion skins. Remove it from the heat and allow it to cool and then strain the liquid form the skins.
The dyeing process is then done. The mordanted and completely wetted fabric is put into the now cool dye bath. Replace the heat under the dye bath, bring the temperature to a boiling point and then immediately decrease the heat to 82°C and simmer for 45 minutes or until the wool has gained the required color. Remove the wool from the dye bath if no further process of dyeing is needed, or allow the fabric to cool with the liquid in the dye bath. Do not cool it with cold water to get quick results. When the skein of wool is cool, rinse it carefully by changing the water quite a few times until the water is clear, and then clean the skein of wool in soapy water, rinse and allow it to dry.
Batik
Batik is a starch resist-dyeing method developed in Indonesia. In this technique, to avoid the color entering certain areas of the fabric these areas are covered with molten wax. The fabric is starched before the design is being drawn upon it. The wax is applied with a type of cup with a fine pouring spout, normally made of copper. Batik paintings, as well as sarongs and lengths of fabric are made. When the fabric is dyed, all waxed areas resist the dyestuff. The wax is then removed by putting the fabric in boiling water.
Tie-Dyeing
Tie-dyeing is a well known artesian dyeing method. In this resist-dyeing process, waxed thread is tightly tied around the areas selected to resist the colored dyestuff, and the fabric is dipped into the dye. The waxed thread is then removed and the fabric is dried. For each color to be added, this procedure is repeated.
Obtaining Odd Colors
Colors other than those obtained by simply using a single dye can be obtained by mixing dyes or dyeing a fabric more than once in various dye baths.
Herbal Wear
Nowadays, herbal wear is also gaining a lot of importance due to its availability at cheaper rate and as garments used as medicine because of their medicinal properties. Generally, garments dyed with natural elements or plants, roots, seeds, flowers, leaves are called herbal wear. Herbal wear has medicinal properties:
. It is anti-allergic.
. It is anti-microbial.
. It has antiseptic properties.
. Such garments have a good breathability.
. The fabric is also eco-friendly as the waste from such herbal dyeing can be transformed into manure.
. It provides pollution free environment.
Vegetable Dyes
Vegetable dyes are not new products. They have been used since many years in India and other countries for dyeing clothes and making paintings. In recent time, the significance of vegetable dyes has increased with much awareness about the harmful effects of chemical dyes. Mainly, Azo group of dyes and Naphthalene based dyes are reflected. Besides, European countries and USA have completely banned production and application of such synthetic colors. Really there is a huge prospect for Vegetable dyes since all of them are obtained from natural sources and are have no harmful effects. Production wise, they are simply biodegradable and pollution free.
Copyright © 2006
The Author:
Fibre2fashion.com – Leading B2B Portal and Marketplace of Global Textile, Apparel and Fashion Industry offers Free Industry Articles, Textile Articles, Fashion Articles, Industry Reports, Technology Article, Case Studies, Textile Industry News Articles, Latest Fashion Trends, Textile Market Trends Reports and Global Industry Analysis.
Can you store the dyes after you have dyed fabric or do they have to be thrown out?
I am specifically talking about lake kelp, bog moss, cranberries and black walnut hulls.
Thanks for letting me know.
It seems like eco-friendly fabric dyes are becoming popular nowadays, especially for restaurateurs and hoteliers. When it comes to customer service, the hospitality industry also aims to seek the overall safety of their customers, and that would include health. Chemicals in most dyes nowadays are being linked to poor health, so I think natural dyes is being favored by many business owners.
Hello
I read with great interest about the mordants, and a few resulting doubts. It seems that mordants are essential, yet they are the most metal based in the recipe. Are they all 100% harmless to human skin?