Felting, Fulling, or Boiled Wool?
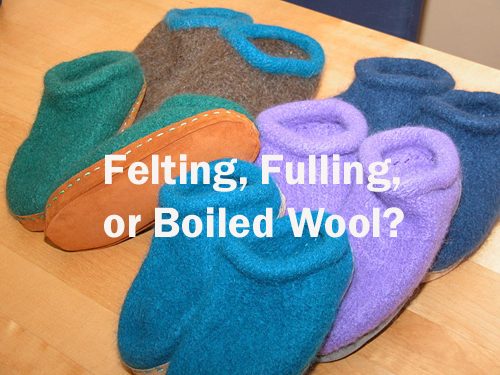
To ignore one of the basic knitting commandments, “Thou shalt not put wool into hot water” is to risk suffering the dreaded consequence of such action – very small, very stiff, little sweaters into which no family member would ever want to grow. But approaching the hot water as friend not foe, affords an opportunity to enjoy a wonderful new perspective on rows of knit and purl stitches. As a distinct change of texture and appearance results from the felting process, simple stocking stitch knitting can be magically transformed all without knowledge of complicated knitting technique.
Felt is a warm, windproof fabric that despite its matted texture remains remarkably lightweight and soft to the touch. To produce a felt fabric, the basic raw material is always the same but the production method can vary. The raw material that is common to all methods is a protein fiber derived from an animal source, most often wool. Other protein fibers such as mohair, angora, alpaca, and some furs can also be successfully felted. Why only animal fibers? It is because these fibers have a unique surface structure which consists of overlapping scales. These scales in reaction to being plunged into hot water, open up and latch on to each other creating new formations. This interlocking process is further aided by rubbing the scales together through some form of agitation such as kneading by hand or the action of a washing machine. Further scale mixing is achieved by making the scales slippery with the aid of a sudsy, soapy solution. Once these scales have found their new positions on the surface of the fabric, there is no going back. These newly-positioned scales remain locked together in their latest relationships and the happy result is felt.
Felting
“Felting” is the term most often used to define the transformation of a protein fiber into this warm and wonderful fabric. In the strictest sense, felting describes the procedure of taking batts of wool fleece (raw wool that has not yet been spun into yarn), adding hot, soapy water and kneading the wool batt until the fiber scales interlock. The word “filz” is found in Old High German. This language was in use prior to the 12th century, an indication that when felting today we are continuing to explore a very ancient craft.
Fulling
“Fulling” is the process of producing felt fabric from animal fiber yarn that has already been woven or knitted. Fulling takes the woven or knitted fabric through the process of hot water and agitation in order to facilitate shrinkage and create felted fabric. In the Middle Ages, “fullers” were textile workers who used Fuller’s Earth, a highly absorptive clay that removed grease and oils from the woven cloth. The agitation of the cleansing action would shrink and matte the fibers creating a fabric that would not unravel. The term fulling stems from “fullare”, a Medieval Latin word meaning “to walk on or trample”. This process emphasizes the agitation that is required in coaxing those fiber scales to intertwine. Today, it is more common to see Fuller’s Earth used as an ingredient in a cosmetic face mask, where it sets its shrinking powers to other tasks.
Baked Wool
“Boiled Wool” is another descriptive term for felted cloth. It is the characteristic fabric produced in Austria and used to fashion chic Tyrolean jackets embellished with braid binding and pewter buttons. Again, the basic raw material is wool yarn. The process is the same as fulling but completed on an industrial level in order to facilitate the handling of larger quantities. Computerized controls finely tune water temperature levels and agitation strength in order to produce a consistent result. The yarn is first dyed, then knit and shrunk without the aid of chemicals. This process produces felt fabric available by the yard, ready for cutting into pattern pieces to be assembled into garments.
Allow yourself time to experiment with the felting process and how the knitted yarn reacts. Knit test samples of stocking stitch in a pure wool yarn. One caution must be observed. Do not use a wool yarn that has been processed as a super-wash yarn, in other words a yarn that can be machine-washed without fear of shrinkage. Since it is shrinkage that is the goal in felting, these yarns are not suitable for felting projects. Knit a number of samples, perhaps in different yarn weights and colors, while making note of the knitted measurements of each. Place these samples in the hot water cycle of the washing machine, removing after the rinse and spin dry cycles. Square up the edges of the samples and allow to dry flat. Measure the samples again and compare to the original measurements. If felting has taken place, it is not only indicated by the change of measurements but in the texture of the fabric. Holding up the felted fabric sample to a strong light, one should barely be able to distinguish the grid of stitches and rows. The felted sample should be very matted and if you cut the knitting, it will not unravel. Notice that the knitting remains soft and lightweight, not stiff and harsh.
If you have moved on to transforming your hand knitting into a felted garment, you may think that is has gone through the most vigorous and tortured wash that knitted yarn could ever endure. Now and forever more, you assume that you can throw that felted garment into the hot wash cycle. Treat your felted garment with “wool rules”. Hand wash using a mild soap or wool detergent in lukewarm water and do not rub or leave to soak as further felting may occur. After thorough rinsing, dry flat. Felted hand knitting can always be improved with brushing and even a light pressing with a warm iron to produce a smoother surface appearance. If you are storing felted garments for an extended length of time, be sure to tuck a moth repellent inside the garment.
These are the basic guidelines to start you down the felted path. If you take the plunge and experiment with different yarn weights, brands and colors, you will increase your knowledge of what really happens when a particular yarn meets hot water. After all, the knitting is easy and the results can be spectacular.
The Author:
Maddy Cranley is a professional knitwear designer, who has created exclusive designs for knitting and craft magazines, authored and published three books on the subject of creating felt garments and projects from hand knitting, and produces an ever-growing line of maddy laine and maddy baby hand knitting patterns. For additional information, see http://www.maddycraft.com